Process
and capabilities
A high-performance
process
Blow molding is a process that creates hollow plastic parts such as bottle containers, gas tanks and kayaks. Thermoplastic material is fed through a hopper, melted and extruded vertically into a tube called a parison. Compressed air then inflates the parison and fills the cavity of the aluminum mold. The plastic part is cooled by the mold and then trimmed of any excess material. This flash material is ground up and recycled to be reused in the production of another part so no waste is produced. See the video below for an overview of the process.
WIDE RANGE OF POSSIBILITIES
We have a wide range of accumulator head extrusion blow molding machines that can make plastic parts from 5 lbs up to 100 lbs shot capacity. We have many similar machines, so we have the flexibility to make the same parts on multiple machines so you never run out of parts.
MULTILAYER OFFERS BEST OF BOTH WORLDS
Lefko is also equipped with multi-layer co-extrusion blow molding machines to minimize fuel vapor permeation or to use post consumer recycled plastic (PCR) material in one of the layers while using an outside virgin resin for its mechanical properties and superior aesthetics. We can also use the best of 2 or more material properties by combining them in the manufactured parts.
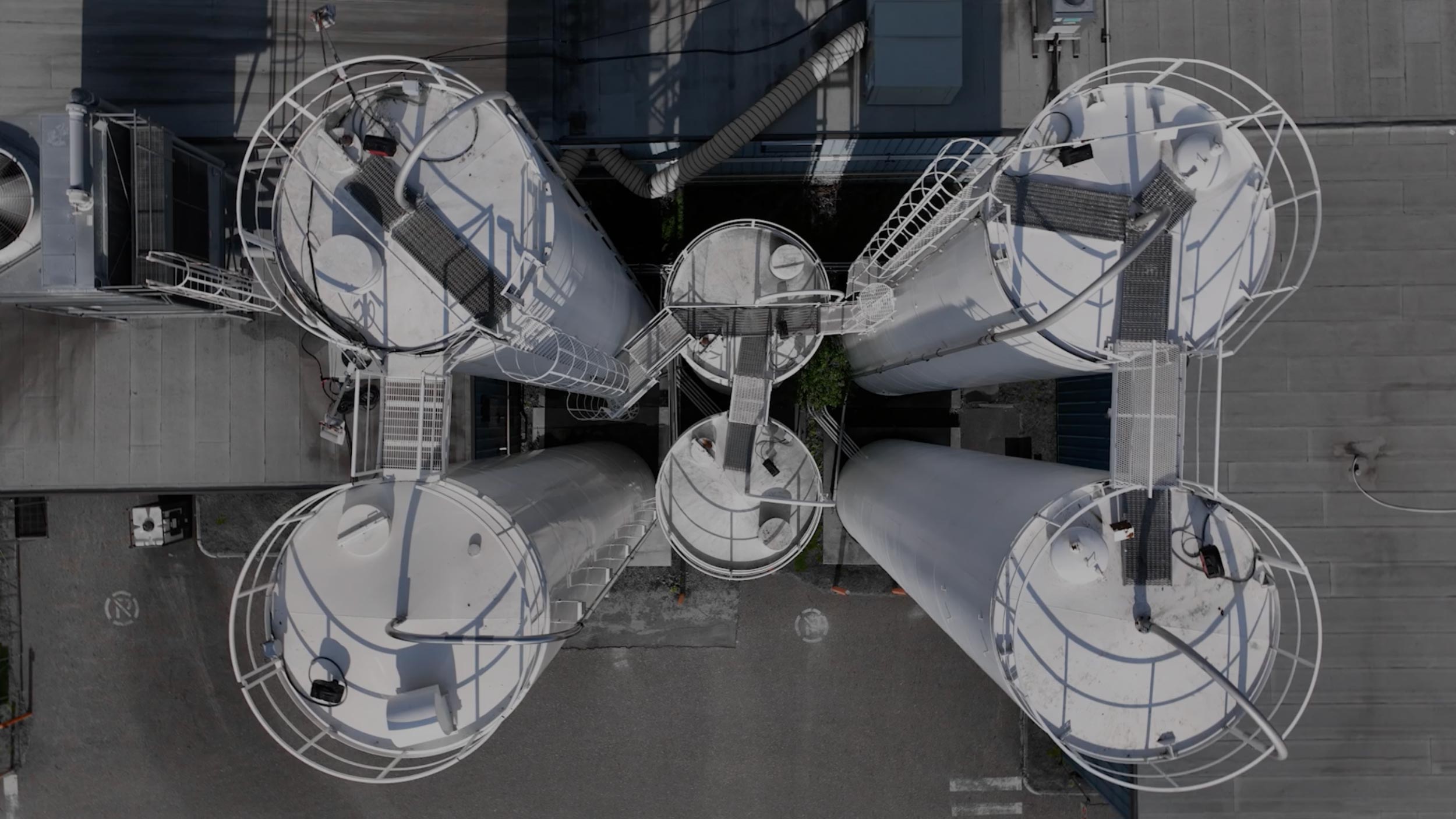
Blow molding
Technologies
Lefko has experience with any type of engineered resins and multiple blow molding technologies.
Of course, we can make monolayer parts that are very efficient vs other production methods (see table below and animation beside).
But we also make highly cost-effective fuel tanks by using a nanocomposite blend called Hyperier® . We’ve produced more than 2M of those over 15 years without any field issues.
And recently, we’ve acquired a multilayer machine, so we can also make 6 layers fuel tanks which achieve the best permeation results of any technology.
Finally, investing in this multilayer equipment shows our dedication to the environment as we can now offer a PCR layer (post consumer recycled material) within virgin layers of material to make the products look brand new, but achieving true circular economy.
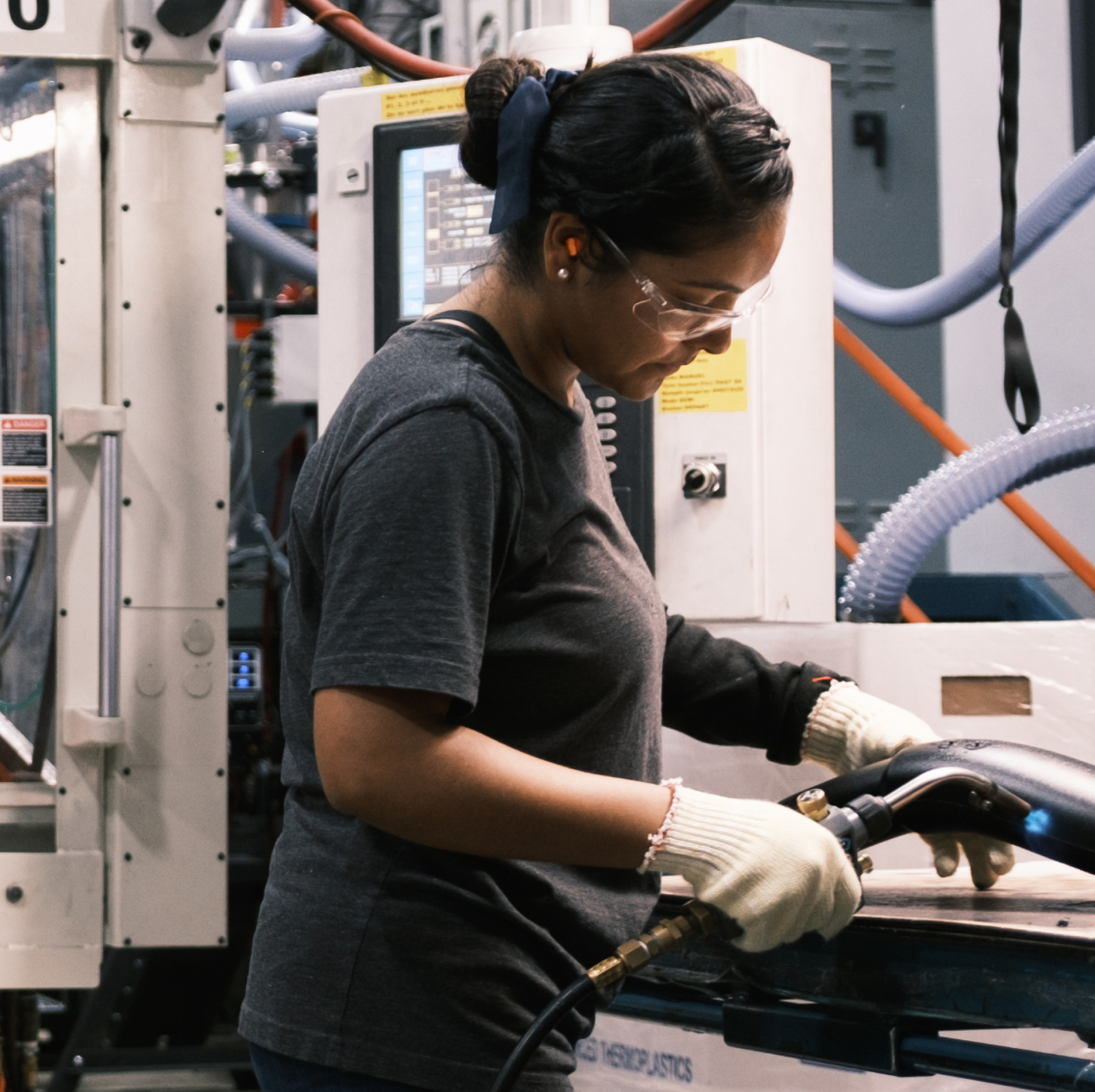
Blow molding
advantages
- Fast cycle times allows for lower part price than other processes like rotomoulding (50% on average)
- Lightweight
- Rigidity vs. injection and ease of assembly
- Smooth surface finish allows for easy cleaning of the components (best for medical applications)
- Blow molded parts can be used to contain (liquid, PU foam, etc.), circulate (air, liquid, etc.) and support (inherent mechanical structure for seats, floating docks, etc.)
- Single or double walled parts
- Solid tabs can be integrated on the side of the parts
- Plastic or metal inserts can be molded in the blow molded parts
- No wasted material, all process scraps are reused or recycled
Moderate to high for Blow
Molding production volume
BLOW MOLDING | THERMOFORMING | ROTATIONAL MOLDING | INJECTION | |
---|---|---|---|---|
COST of mold | Moderate | Low | Low – Moderate |
High |
COST of mold touchups | Moderate | Moderate | Moderate | High |
COST of part | Low – Moderate |
High | High | Low |
PRODUCTION speed | Moderate – High |
Moderate | Low | High |
PRODUCTION volume | Low – High |
Low – Moderate |
Low – Moderate |
High |